News
Nissan begins UK production of the new Qashqai
We go behind the scenes at Nissan’s Sunderland Plant to discover how one of the UK’s most popular cars is built
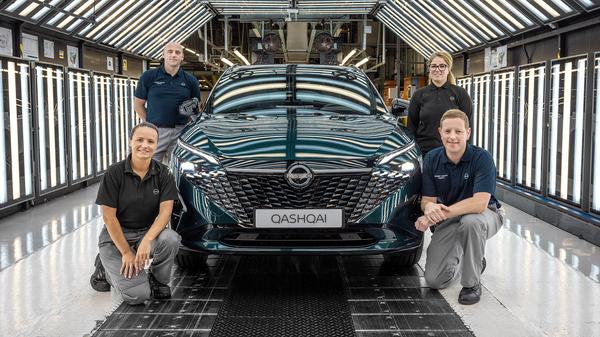

Words by: Catherine King
Published on 28 May 2024 | 0 min read
Nissan is very proud of its Qashqai and for good reason. Back in 2006 it shaped the SUV segment as we know it today, arguably inventing the concept of a crossover altogether. In total 4.4 million Qashqais have been built at Nissan’s UK factory in Sunderland, with nearly three quarters of a million sold here and the rest finding homes in more than 100 countries. It’s so popular that you are generally never more than about 500m from a Qashqai in the UK, and Nissan is hoping the updates to the latest version will continue the appeal. As production of the facelifted Qashqai begins, Nissan took the opportunity to show us how to build a best-seller.
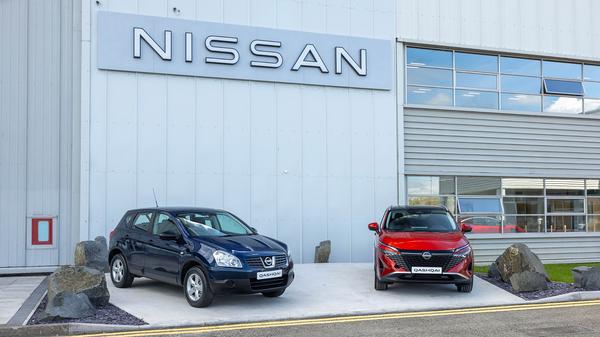
Starting with long metal coils and ending with a fully formed car, the full process takes 14 hours end-to-end, with a new Qashqai born approximately every two minutes. The process is heavily automated with Automated Guided Vehicles (AGVs) buzzing around delivering components, huge robotic arms welding panels together while other robots paint cars in different colours without cross contamination. Yet so much of the process requires a human touch. We started our tour in the Recruitment Centre with a skills test to see if we had what it takes to build a Qashqai. This gave a sense of the intricate web of wires and bolts hidden behind the plush dashboards of the finished cars.
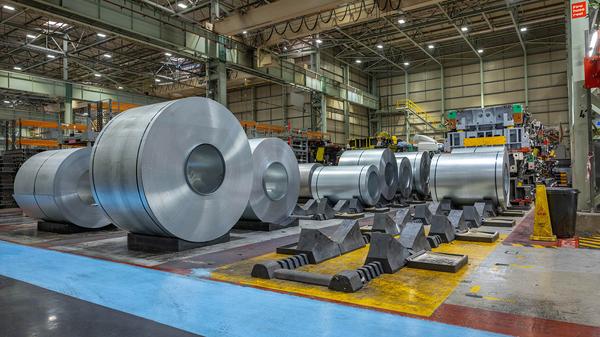
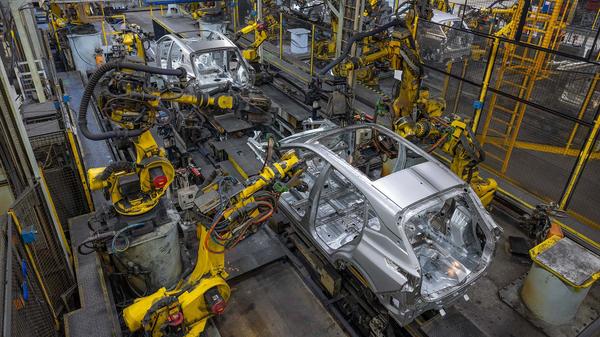
As our tour progressed we learnt more about the process and how some things simply can’t be done by a machine. While 1,052 robots assemble the shells of the Qashqai, the final fit and finish is completed by hand before the cars head to the Paint Shop. It’s a delicate procedure with tolerances as little as 0.1mm and it’s just part of nearly 1,000 quality checks each Qashqai undergoes.
Then there’s the cars with two-tone paintwork. Once the first colour is added, it requires a highly skilled worker to carefully mask panels to protect parts of the bodywork before the second colour can be applied. The final stop for painted cars is the Trim and Chassis department. This is home to the biggest team at the plant, with employees responsible for fitting out the interiors, attaching the wiring harnesses, and marrying the body of the cars to the drivetrain. Three and a half hours after the painted shells arrive from the Body Shop the finished Qashqais are ready to hit the road following a final round of quality checks.
Then there’s the cars with two-tone paintwork. Once the first colour is added, it requires a highly skilled worker to carefully mask panels to protect parts of the bodywork before the second colour can be applied. The final stop for painted cars is the Trim and Chassis department. This is home to the biggest team at the plant, with employees responsible for fitting out the interiors, attaching the wiring harnesses, and marrying the body of the cars to the drivetrain. Three and a half hours after the painted shells arrive from the Body Shop the finished Qashqais are ready to hit the road following a final round of quality checks.
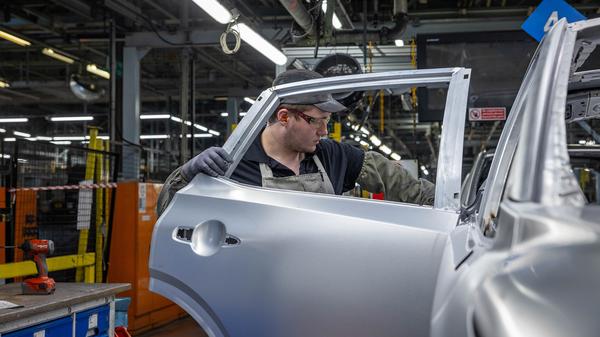
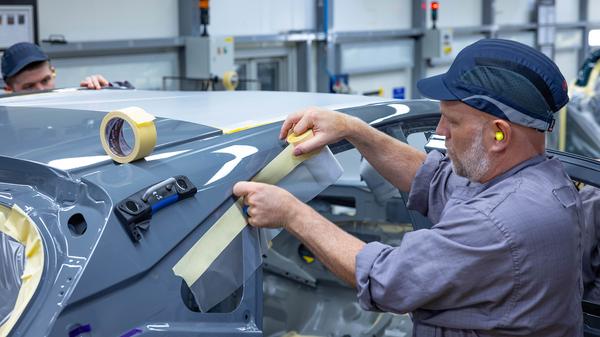
Nissan has been building cars in Sunderland since the plant opened in 1986 with 430 members of staff, nine of whom still work at Nissan today. The sheer scale of how the enterprise has grown is difficult to get your head around, even after completing a four-hour tour of the facility. Nissan has invested over £1bn to build the Qashqai in the UK and now supports 6,000 jobs at the plant and approximately 30,000 jobs in the wider supply chain. This huge logistics operation sees around one million parts delivered to the plant daily and Nissan says since 2006 it has contributed an average of £2.8bn to the UK economy per year.
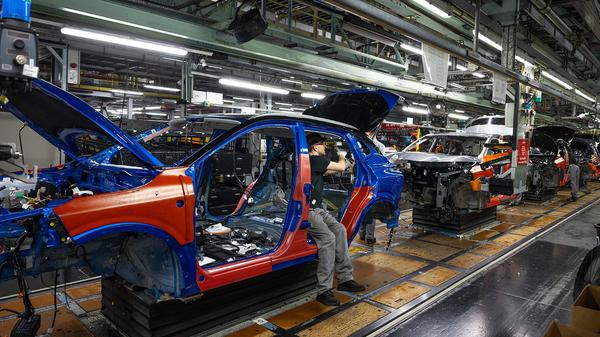
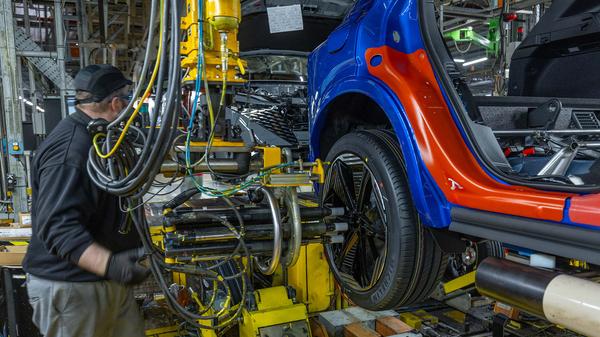
That’s big business indeed, but how is Nissan approaching the move to electrification? Currently the plant assembles batteries on-site for the Juke hybrid and Qashqai e-power, but production of the existing generation of the Leaf has just ended. However, at the end of last year Nissan announced its EV36ZERO strategy laying out its plan heading towards 2030. This includes a £3bn investment into the Sunderland plant to build three new all-electric models and a ‘Gigafactory’ to futureproof the plant and protect jobs in the UK automotive sector for years to come.
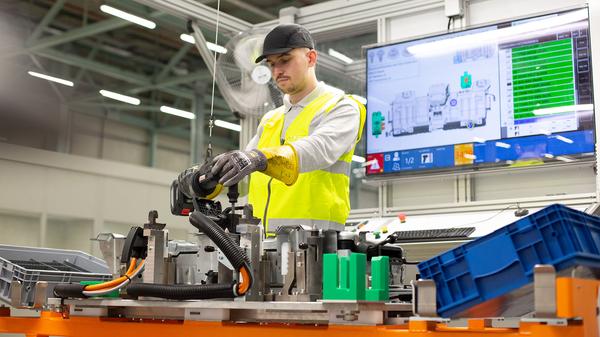
But what does this mean for Britain’s beloved Qashqai? We know one of the three new EVs will be the next generation of Qashqai, although Nissan has yet to confirm if it will wear the Qashqai name. The production line will remain flexible with the ability to build hybrids alongside fully electric cars, so while Nissan hopes to go fully electric in Europe, it’s possible the Qashqai as we know it could live on in other markets for a little longer.
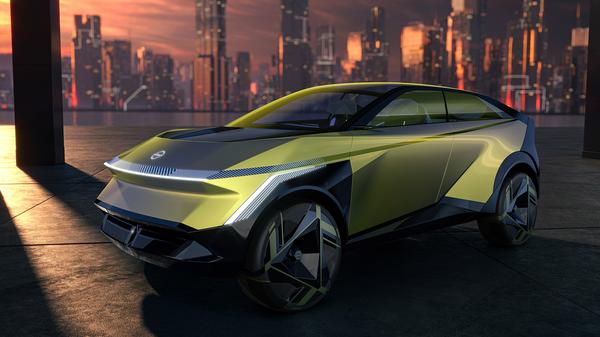